With the February edition of Professional Builder, I begin a series on the evolution of quality management. Here is a more detailed version of an excerpt from that article to come. Be sure to read that.
Can a company really go from worst to first in quality, turn their reputation around, bring customers back in droves and make money doing it? In the late 70’s Ford introduced the Fairmont, a new midsize car developed to fend off the burgeoning Japanese competition that was eating the Big Three’s collective lunch. This followed the sad era of the Ford Maverick, Plymouth Duster and Chevy Vega. Back then I used to joke about opening a dealership featuring those 3 vehicles and call it, “The Worst of Detroit.” This vehicle was supposed to be, “The One.” Ford bought serious ad time for SuperBowl XIV in 1980 (Steelers 31 – Rams 19) and ran a spot that has stuck with me for more than 30 years. It showed the Fairmont coming down a production line full of happy workers, all smiling and apparently thrilled to be building this swell new car. At the end of the line, small windows began popping up around the screen, circling the Fairmont, as a machine gun-like sound fired in the background. Each of the 21 windows displayed a white-coated inspector with clipboard and checklist in hand. Meanwhile, the narrator of the commercial boasted that each Fairmont went through 21 inspection stations, thus assuring the quality of the vehicle. TWENTY ONE SETS OF EYES!
The average American in 1980 was impressed by this. More inspections had to mean better quality, right? At the time, I was a quality process manager for Motorola. Motorola was in the process of recovering from their failing consumer electronics business and became a true pioneer of the quality reformation movement in this country during the 80’s and 90’s. Although young, (very young,) I had learned enough to know the futility of Ford’s quality-by-inspection approach. We were studying Japanese quality and knew that Toyota, for example, had only 3 inspectors per line, while 21 was typical for U.S. manufacturers. Ponder that; Ford invested in 18 extra employees and Toyota’s quality still put the Fairmont to shame. How could that be? Hint: it was not the quality of the workers.
I made frequent trips to Motorola’s small Albuquerque plant in those days. It served as a test cell for many of our process and quality improvement efforts. On my next trip following the SuperBowl I left Hertz in a brand new Ford Fairmont.Coincidence? I had arrived late in the evening, very tired, and while searching for my hotel I missed a street and had to turn around in a parking lot. During that turn at a normal speed, I hit a small pothole. WHAM! The initial sound was followed by a deafening chatter that worsened when I slammed on the brakes. Steam rose out from the grill and a dent formed in the hood, from underneath. Shutdown and further inspection revealed that this minor meet-up with a pothole had completely detached the radiator and fan-shroud assembly from its mounting and sent it into the fan blades which in turn sent the shroud into the hood from below. As I waited for the Hertz tow-truck to arrive and return me to the airport to get another car, I ruefully wondered if perhaps 22 inspectors might have prevented this problem. Right.
I have retold that story over the years to illustrate the fallacy of “quality by inspection.” The sad thing is that when I arrived in the homebuilding industry full-time 23 years ago, inspection-based quality would have been a great leap forward for most builders. Today, 30 years following my Albuquerque incident, virtually all cars and American autos in particular have made an order of magnitude improvement in quality. Ford and GM now compete head-to-head with Japanese and Korean brands in surveys such as JD Power and ratings by Consumer Reports, while the European brands struggle to keep up. The Ford Fusion, to cite just one example, was recently cited by Consumer Reports as having better reliability than the Toyota Camry or Honda Accord. Just a decade ago, that was unthinkable. Baby boomers will recall how rarely their parents’ cars made it to 100,000 miles while today it is routine. What changed?
Here’s the kicker. As a percent of income, today’s dramatically better vehicles – with power-everything on even the smallest econobox, great sound systems, electronic controls and bodies that seem to never rust – cost us about exactly the same as the crummy cars from the 70’s and 80’s. That was not achieved by adding that 22nd inspector. Enter any domestic auto plant today and inspectors are very hard to find. The U.S. automotive industry has made a remarkable turnaround. All the Big Three are now profitable and building great cars. I know because I rent on average more than 50 cars a year. Both Chrysler and GM have paid back the great majority of their government loans which are now looking like a pretty good investment, with an estimated 2.4 – 3 million jobs saved in total, and all of them paying taxes and staying off of welfare roles. A great comeback story.
So how does homebuilding compare? Can we have a similar experience? Be sure to pick up my February article to find out.
About the Author
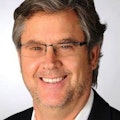
Scott Sedam
Scott Sedam, president of TrueNorth Development (www.truen.com), spends most of his time working in the trenches with builders, suppliers and trade contractors. His Lean Builder blog appears weekly at HousingZone.com. He welcomes your feedback at [email protected].