The key benefits of lean and six sigma include providing structured methods of improvement to reduce waste, shorten production time, reducing cost, reducing lead times, promoting concurrent work, accelerating activities, improving planning and control and ultimately high levels of customer satisfaction.
An essential element to making lean and six-sigma work is in ensuring that its practices are used beyond production. From land development, marketing, sales, estimating, design, purchasing, construction, warranty and service to finance and administration all need to be introduced to the concepts.
WASTE
One of the key issues to address for lean is waste and these can be addressed via the partnerships and process mapping discussed above. This includes
- Overproduction
- Excessive and wasted motion
- Excessive or missing inventory
- Inefficient transportation
- Waiting and delays
- Defects scrap and rework
- Over processing
What are YOUR costs of waste, defects, rework and warranty?
These categories of waste are to some degree in and off themselves a shift in thinking, in many ways we build in delays and transportation issues to our construction schedules. But by addressing each of these in tandem with flow charts, value stream mapping for example we can begin to identify and drive out waste, reduce time lines and institute Just In Time delivery of materials and products. For example while motion studies are more common in manufacturing settings they are applicable for construction. This can relate to studies of the construction site layout for storage of materials and equipment to ensure the least transport on site for example. This can also relate to each floor or section of a building under construction.
5S
Another lean tool is 5S. This includes combining the concepts of
- Sorting
- Systematic arrangement
- Spick and Span
- Standardization
- Self-discipline
Again this can easily be related to the construction site to ensure that materials are stored appropriately for example on pallets so they are off the ground and covered for protection from rain or ground water. Even tools and equipment in trucks and in toolboxes or especially wheeled tools cabinets can be organized to reduce damage and ease of location during work. It most certainly applies to warehousing of equipment and materials.
While all of the above are elements of lean they can all be coordinated especially on a problem solution or improvement project level by using the six sigma concept of Define, Measure, Analyze, Improve and Control (DMAIC). This can be used as a five-step improvement process much in the same way as Plan, Do, Check, Act (PDCA). This can be used to address individual problems that have occurred or for preventive actions. Or it can be used as a wider improvement project or initiative framework to help lead and coordinate. This is a simple but effective way to introduce a concept of six sigma.
AREAS OF LEAN TO FOCUS ON
Some elements to think about when using lean for improvement ideas include the following:
- Remove intermediaries
- Use substitution
- Reduce or recycle
- Eliminate the things that are not used or necessary
- Do tasks in parallel
- Smooth work flow
- Minimize hand offs
- Use pull systems
- Develop alliances
- Implement cross training
- Optimize the level of inspection
- Focus on preventive maintenance of tools and equipment
- Standardize
- Develop contingency plans
- Reduce the number of components
- Use visual job site displays to communicate project information
While this is just an overview, it does relate how even small steps can be taken to implement key elements of lean and six sigma in the construction setting.
NEXT TIME, Improving Customer Satisfaction through Employee Satisfaction & Schedule of Upcoming Topics
About the Author
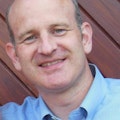
Denis Leonard
Denis Leonard has a degree in construction engineering an M.B.A. and a Ph.D. in quality management. Denis is a Fellow of the American Society for Quality, a Certified Quality Manager, Auditor and Six Sigma Black Belt. He has been an Examiner for the Baldrige National Quality Award Board of Examiners a Judge on the International Team Excellence Competition and a Lead Judge on the National Housing Quality Award. A former Professor of Quality at the University of Wisconsin, he has experience as a quality manager in the homebuilding industry as well as construction engineer, site manager and in training, auditing and consulting with expertise in strategic and operational quality improvement initiatives. His work has achieved national quality, environmental and safety management awards for clients.
Denis is co-author of 'The Executive Guide to Understanding and Implementing the Baldrige Criteria: Improve Revenue and Create Organizational Excellence'.
http://www.BusinessExcellenceConsulting.net
Full listing of blogs https://www.probuilder.com/author/denis-leonard