A tool referred to as the “Quality Life Cycle” provides a strategic mechanism to chart and sustain quality while proactively countering shortcomings of its implementation, such as stagnation and limited application, which can ultimately result in failure. The quality life cycle was developed as part of a UK and US research study, allows for the characterization and visualization of the various complex stages and dynamics of quality. It allows charting of not only the current status of quality in an organization but also its historical development or life cycle. The historical data provide an aid for learning based on past strategic decisions and the resulting impacts. In addition, the quality life cycle can be used to develop scenario planning to assist in determining the most effective course of action for future strategies. In this regard the quality life cycle promotes strategic thinking and aids in the strategic decision making process. Strategic decision making is achieved by using a timeline to identify six key stages of quality system application (such as the implementation of new initiatives), the methods or systems used (such as ISO 9001) and their success. Each stage is then represented by a quality life cycle element, as defined in the following:
The life cycle elements are:
1. Adoption: the implementation stage of a new quality initiative.
2. Regeneration: when a new quality initiative is used in conjunction with an existing one to generate new energy and impact.
3. Energizing: when an existing quality initiative is refocused and given new resources.
4. Maturation: when quality is strategically aligned and deployed across the organization.
5. Limitation or stagnation: when quality has not been strategically driven or aligned.
6. Decline: When a quality initiative has had a limited impact and is failing and potentially awaiting termination.
Figure 1shows a generic graphical representation of how each of these elements.
However there is no set sequential format for these elements, as this is not a prescriptive model. Nor does the quality life cycle dictate the type of quality management tools or techniques to be applied. Each case should be based on the most appropriate tool for a particular organization, depending on its history, culture, needs and capabilities.
Companies tracked using this model include one that has successfully sustained quality for over a 20 year period having experienced all of the life cycle elements including decline, which it overcame by energizing and then continued successfully on with its quality journey.
What does your quality journey look like mapped out on the quality lifecycle?
Where are you now?
How can the life cycle help you to scenario plan for the future?
Are you stagnating or in decline?
Is it time to energize or regenerate your quality efforts?
(The Quality Lifecycle, Denis Leonard & Rodney McAdam, Quality Progress, Aug 2003, pp50-55)
About the Author
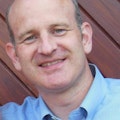
Denis Leonard
Denis Leonard has a degree in construction engineering an M.B.A. and a Ph.D. in quality management. Denis is a Fellow of the American Society for Quality, a Certified Quality Manager, Auditor and Six Sigma Black Belt. He has been an Examiner for the Baldrige National Quality Award Board of Examiners a Judge on the International Team Excellence Competition and a Lead Judge on the National Housing Quality Award. A former Professor of Quality at the University of Wisconsin, he has experience as a quality manager in the homebuilding industry as well as construction engineer, site manager and in training, auditing and consulting with expertise in strategic and operational quality improvement initiatives. His work has achieved national quality, environmental and safety management awards for clients.
Denis is co-author of 'The Executive Guide to Understanding and Implementing the Baldrige Criteria: Improve Revenue and Create Organizational Excellence'.
http://www.BusinessExcellenceConsulting.net
Full listing of blogs https://www.probuilder.com/author/denis-leonard